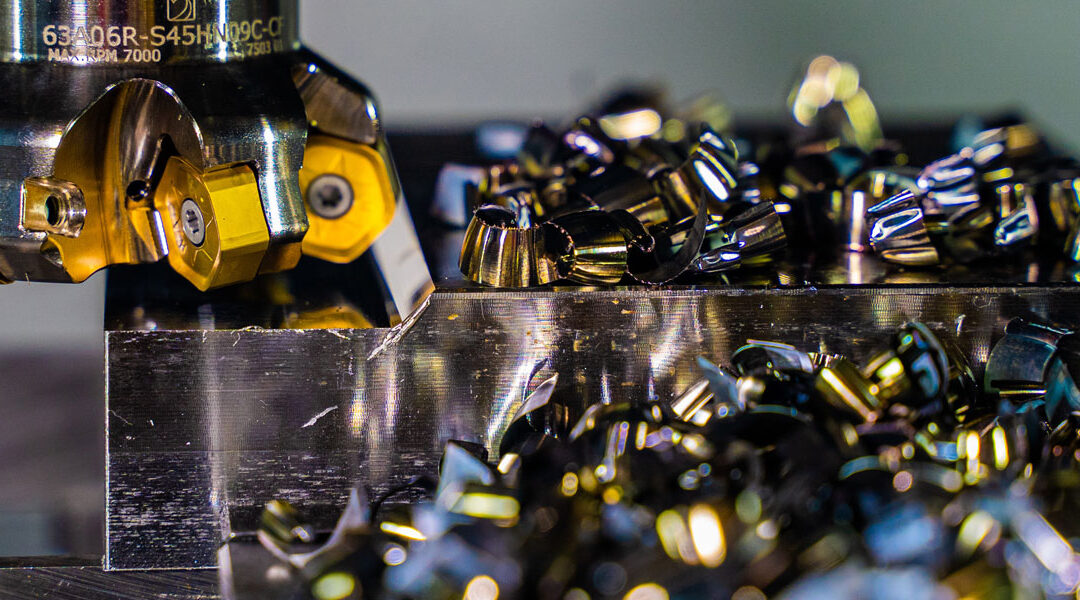
پس از انتخاب سیال سنگ زنی مناسب و سیستم مدیریت آن، اولویت بعدی نحوه تزریق صحیح سیال سنگ زنی به ناحیه آسیاب می باشد. سیال سنگ زنی باید به جای اینکه صرفاً در محل اتصال قطعه کار و چرخ سنگ زنی باشد، به ناحیه قوس برش تزریق شود. به طور کلی، تنها بخش کوچکی از مایع خنک کننده ریخته شده وارد می شودبرش دادنناحیه قوس چرخ سنگ زنی چرخان مانند یک دمنده عمل می کند تا سیال سنگ زنی را از دایره بیرونی چرخ سنگ زنی پرتاب کند.
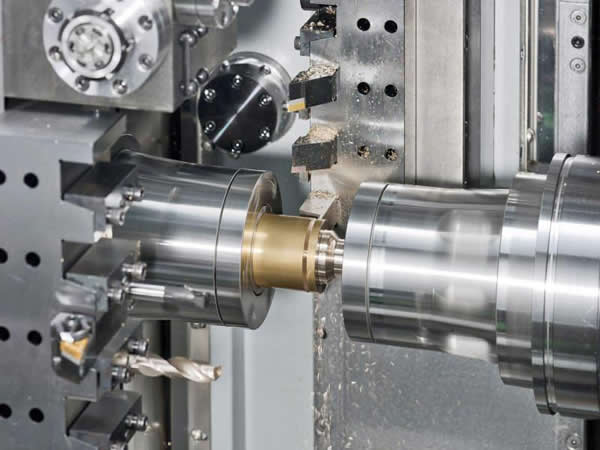
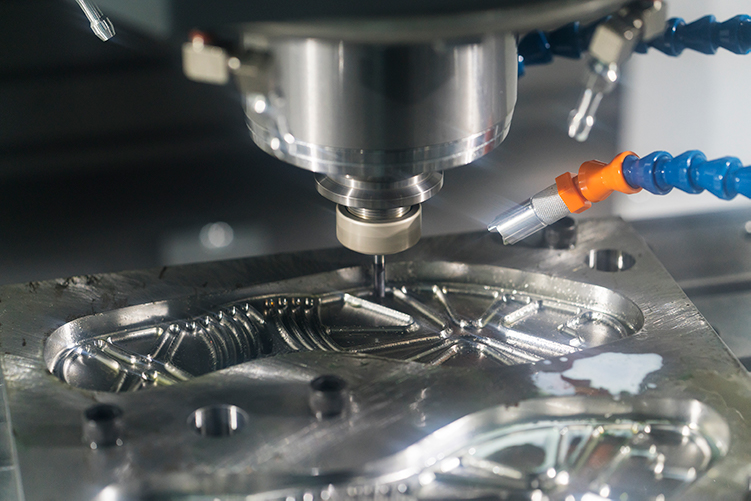
سوراخ ازچرخ سنگ زنینه تنها می تواند تراشه ها را نگه دارد، بلکه مایع سنگ زنی را نیز حمل می کند. به این ترتیب سیال سنگ زنی توسط خود چرخ سنگ زنی به ناحیه قوس برش وارد می شود. بنابراین، با سرعت مناسب، سیال سنگ زنی که در دایره بیرونی چرخ سنگ زنی ریخته می شود، به قوس برش می رسد. علاوه بر این، نازل باید به گونه ای طراحی شود که سیال سنگ زنی بتواند در نقطه تزریق صحیح با سرعت مناسب تزریق شود. اندازه نازل باید تمام عرض چرخ سنگ زنی را پوشش دهد.
هنگامی که عرض مشخص است، ارتفاع باز شدن (d) نازل را می توان محاسبه کرد. اگر عرض نازل 1.5 باشد، سطح نازل 1.5din2 است. اگر سرعت آسیاب 5500 (1676 متر در دقیقه) باشد، باید در 12 ضرب شود تا به 66000 در دقیقه برسد. بنابراین، سرعت جریان سیال سنگ زنی در نازل عبارت است از: (1.5din2) × 66000in/min=99000din3/min. اگر فشار پمپ روغن 110psi (0.758MPa) باشد، جریان مایع در دقیقه 58 gpm (58 گالن در دقیقه، حدود 219.554 لیتر در دقیقه) و 1 گالن = 231 اینچ مکعب است، بنابراین جریان پمپ روغن 231 in3 × 58gpm است. =13398in3/min.
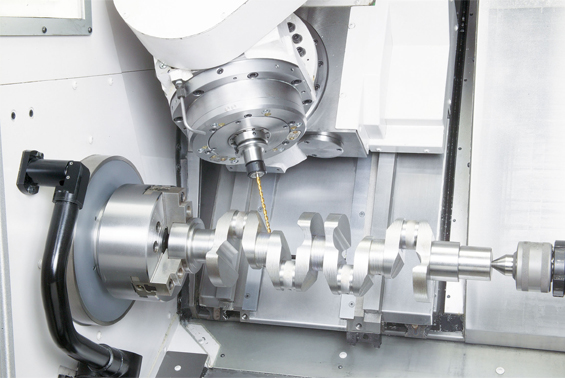
بدیهی است دبی در ورودی و خروجی پمپ روغن باید برابر باشد یعنی 13398 برابر با 99000d باشد. ارتفاع نازل d را می توان 0.135 اینچ (13398/99000) محاسبه کرد. ارتفاع واقعی باز شدن نازل می تواند کمی کمتر از مقدار محاسبه شده باشد، زیرا سرعت سیال سنگ زنی پس از خروج از نازل کاهش می یابد. هنگامی که نازل رو به چرخ سنگ زنی نیست، توجه به این فاکتور بسیار مهم است. بنابراین، اندازه نازل در این مثال 0.12 "×1.5" بهتر است.
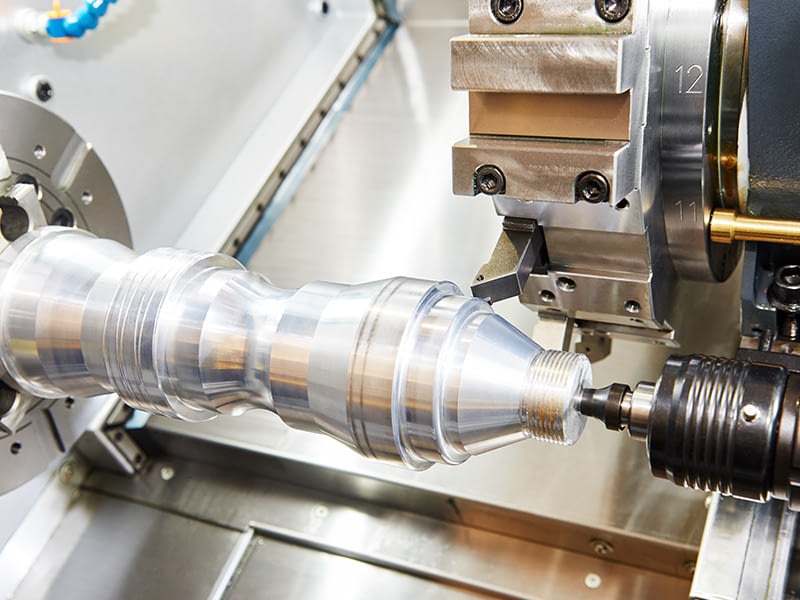
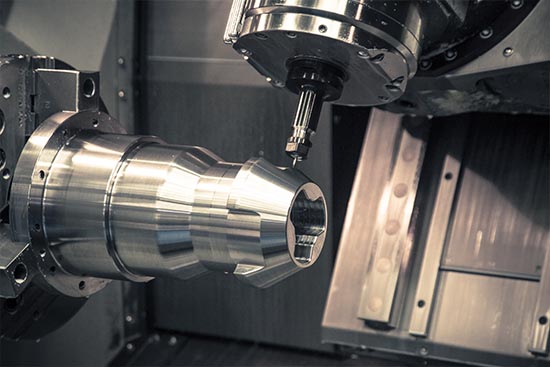
فشار پمپ روغن برای فشار دادن مایع به جریان در سیستم خط لوله است. گاهی اوقات مقاومت سیستم ممکن است 110Psi از فشار نامی پمپ روغن فراتر رود، زیرا نازل اغلب به اشتباه ساخته می شود و خطوط لوله، اتصالات، بازوهای چرخان متحرک و غیره پیچ خورده یا مسدود می شوند.
زمان ارسال: فوریه 13-2023